微細穴あけ加工とは?
微細穴あけ加工は、マシニングセンタ、放電加工機、レーザー加工機などを用いて、ワークに微細な穴をあける技術です。微細穴をあけるためには、より高度な技術と設備が必要になります。
この技術は、医療機器や半導体関連部品など、様々な精密機器の製造において不可欠です。特に製品の小型化が進む中で、その需要は高まっています。したがって、微細穴あけ加工においては、高い技術力と品質が求められます。
昭和製作所では、マシニングセンタ、放電加工機を用いた微細な穴あけを得意としております。長年の経験と知識、そして充実した設備により高品質な加工を実現しています。加工会社をお探しの方は、お気軽にご相談ください。
加工可能な穴のサイズ
加工可能な穴のサイズは、工法やワークの材質などによって異なります。微細穴の場合、明確に寸法は定められていませんが、おおよそφ0.1mm以下を微細穴とすることが多いです。
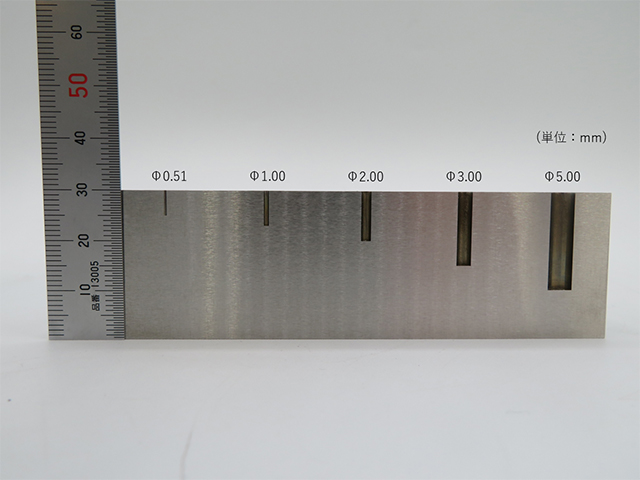
図:穴径サンプル断面
ただし、上記の理由から対応サイズは会社によって異なります。そのため、「微細穴」と表記されていても、ご希望のサイズの穴に対応していない場合もありますのでご注意ください。まずは、ご依頼を検討している会社に、直接お問い合わせをされるのがよいでしょう。
微細穴あけ加工はどんな部品・製品に用いられるのか
微細穴あけ加工の技術は、以下のような製品・機器の部品などに用いられています。
- 医療機器
- 半導体
- 時計
- 自動車
- 輸送機
- 家電製品
- 航空宇宙
- 通信機器
これらを見ると、幅広い分野の製品・機器に微細穴加工が行われているのがおわかりになるでしょう。
昭和製作所は、マシニングセンタ、放電加工による微細穴あけ加工を得意としております。「基準面に対して指定角度で微細穴加工が欲しい」「加工時の熱影響が気になる」等さまざまなニーズに応じて適した工法をご案内いたします。
微細穴あけ加工の代表的な方法と技術
微細な穴あけ加工はさまざまな方法が用いられますが、その中でも代表的な方法を3つご紹介します。
- 切削加工
- ワイヤー放電加工
- レーザー加工
これらの加工は、方法が異なるだけでなく、対応可能な材質も異なります。重要なのは、どのような材質にどのような穴をあけるかに応じて、適した方法を選ぶことです。
ここでは、それぞれの加工方法の特徴と長所、短所を詳しくご説明しますので、どの方法が適しているのか参考にしてください。
切削加工
切削加工は、汎用フライス・汎用旋盤、マニングセンタ・NC旋盤等の機械を使用し、切削工具を用いてワークを削り、穴をあけたりする工法です。
基本的に、ワークの不要な部分を除去しながら図面通りの形状に加工をします。切削加工は精度が高く、深穴をあけることにも適しています。また、比較的安価に穴あけができるという利点もあります。
穴径に対する深さが大きいものや、曲面に穴加工を行いたい場合は、ザグリ加工を施すことで可能になるケースがございますので、お気軽にご相談ください。
長所 |
|
---|---|
短所 |
|
ワイヤー放電加工
ワイヤー放電加工は、放電加工機を使用し、ワイヤー線に電流を流してワークを溶融することで穴をあけることができる工法です。電気を通さなければならないため、通電性のない材料には穴をあけることができません。
長所 |
|
---|---|
短所 |
|
レーザー加工
レーザー加工は、高エネルギー密度のレーザー光線を照射して、ワークを局所的に溶かして穴をあける工法です。ワイヤー放電加工と混同されることがありますが、ワイヤー放電加工は電気を利用して穴をあけるのに対し、レーザー加工は光を利用して穴をあけるため異なります。
長所 |
|
---|---|
短所 |
|
長所・短所を並べると、それぞれ向き不向きがあることがおわかりになるのではないでしょうか。昭和製作所では、放電加工(ワイヤー放電、細穴放電、形彫放電)による微細穴あけ加工も得意としております。もし加工方法にお悩みであれば、昭和製作所へご相談ください。
マシニングセンタによる微細穴あけ加工の事例
微細穴あけ加工にはさまざまな工法がありますが、今回は、昭和製作所が得意とするマシニングセンタによる加工事例をご紹介します。
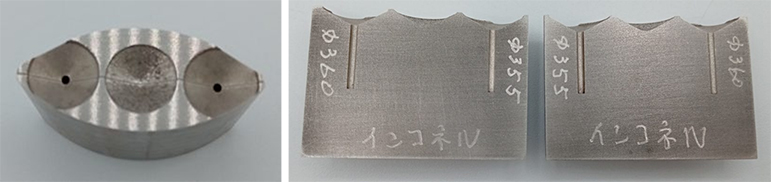
図:インコネル材微細穴加工(Φ1×10mm FBH)
インコネル材は非常に硬い材料ですが、マシニングセンタを用いて切削条件、刃物を適切な選定をすることで、微細穴を精度よくあけることができます。
弊社ではインコネル材を始め、鉄・非鉄問わず様々な素材でもご対応可能です。
マシニングセンタ、ワイヤー放電加工機による微細穴あけ加工の実績をご紹介いたします。
表 材質別加工実績(※一部抜粋)
また、微細穴だけでなく形彫放電加工機を使用することにより、下記の画像のように極小スリットを入れることも可能です。
今回ご紹介した事例はほんの一部です。微細穴・スリットやその他金属加工は昭和製作所にお任せください。
微細穴あけ加工のポイント
微細穴あけ加工のポイントは、材料の性質を十分に考慮することです。なぜなら、加工方法によって適さない材料もあるからです。材料選定の段階で迷われた場合は、ぜひ昭和製作所にご相談ください。ご依頼内容に応じて最適な材料・加工方法をご提案いたします。
測定につきましては、穴径・穴深さ並びにワークの大きさに応じて測定機器を選定いたします。弊社所有、三次元測定機の測定子(プローブ)は最小Φ0.5×3.0mmとなります。
最小プローブでご対応が難しい場合、公共機関の設備を使用しご対応いたします。それでも測定が難しい場合は、試し加工時、試験体を半割りにし測定又は機械加工値での精度保証とさせていただいております。
昭和製作所では、画像測定器や表面粗さ測定機などを保有しています。さらに、昭和製作所はJIS Q 9100の認証※も取得しており、常に品質向上に努めています。
※航空宇宙・防衛産業に特化した品質マネジメントシステム
微細穴あけ加工をご依頼の際は昭和製作所へご相談ください
微細穴あけ加工の方法はさまざまな方法がありますので、頭を悩ませている方もいるのではないでしょうか。今回はその一部をご紹介しましたが、ご参考になれば幸いです。
昭和製作所では、放電加工による微細穴あけ加工を得意としております。弊社が保有している放電加工機についてはこちらでもご紹介しておりますので、あわせてご覧いただくことをおすすめします。
また、先ほどの事例などをご覧になって、より詳しい話を聞きたい、この依頼に対応できるか聞きたいと思われた方は、お気軽に昭和製作所へご相談ください。
【お問い合わせはこちら】
連絡先:03-3764-1621
お問い合わせフォーム