旋盤による段付き加工について
旋盤による段付き加工は、様々な場面で用いられる加工方法です。旋盤という切削加工機で、加工物(ワーク)の一部を削り取り、段付き形状に加工します。段付き加工は旋盤以外の工作機械でもできますが、旋盤を使用する場合は丸物のワークに行うことが多いです。
実際に、どのような部品や製品に段付き加工が施されているのか見てみましょう。
- シャフト
- 軸受
- ピストン
- ナット
- ボルト
場合によっては別の工作機械を用いることもありますが、一般的に上記の部品に段を付ける際は、旋盤を用いて段付き加工を行います。では、段付き加工を行う工作機械「旋盤」はどういった機械なのでしょうか。
旋盤加工とは?
旋盤加工とは、数多くの工作機械の中でも最も基本的な切削加工機の一種となります。
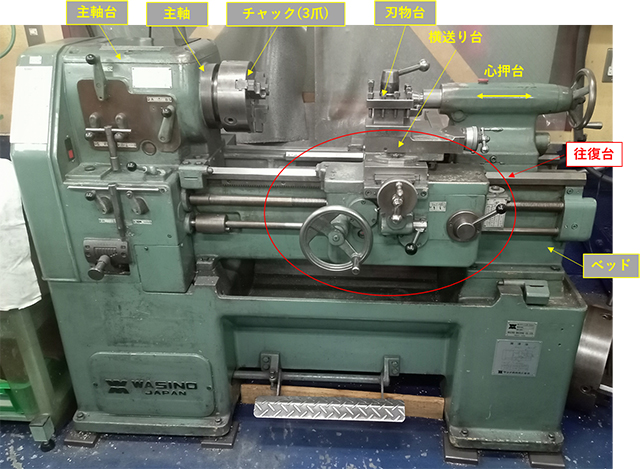
図:汎用旋盤
主軸端に取り付けたチャックと呼ばれる回転する台にワークを取り付け、刃物台に切削工具(バイト)を取り付けます。バイトをワークに押し当て、直進運動をしながら削ります。心押台はベッド上を移動できる構造となっています。センター穴をあけたワークに押し当てることで、ワークの振れ防止、ドリルによるワークへの穴あけ加工ができます。
旋盤加工は円柱、円筒、円錐形状の回転対象部品の製作に適しています。バイトの種類や当て方を変えることで、外径削り(外丸削り)、内径削り、テーパー削り、端面加工、面取り、中ぐり加工、溝入れ、ねじ切り、ローレット加工などを行うことができます。
旋盤の種類は多く、汎用旋盤、立旋盤、NC旋盤、複合旋盤などがあります。製品に応じ、ある程度の形状までは汎用旋盤にて加工を行い、加工精度が高く、複雑な形状の場合は、コンピューターによる数値制御が可能なNC旋盤や複合旋盤を使用します。
機械部品、自動車部品、医療機器など、精密性が求められる部品の製造に適しています。
旋盤加工の特徴をまとめると、以下の通りです。
- 精度高いの切削ができる
- 切削工具の種類や当て方を変えることで、様々な形状の加工が可能
- ワークを回転させるため、丸物に適している
旋盤を用いた段付き加工の種類・方法
旋盤を用いることにより、丸物などを段付き形状にすることができます。その方法はいくつかあり、段の位置や形状によって異なりますが、主に以下の5種類に分類されます。
- 外径加工
- 内径加工
- 端面加工
- ねじ切り加工
- 面取り加工
それぞれ、段の位置や形状、精度、ワークの材質によって適した加工を行うことで、図面通りに仕上げることができます。
今回はS45C材を用いて工程ごと(外径加工→ねじ切り加工→端面加工→C面加工→内径加工)に分けてご紹介いたします。汎用旋盤を使用し、どのように加工をするのか知りたい方は、ご参考になさってください。
また旋盤のみならず、必要に応じて他の工作機械も用いることもあります。昭和製作所では、ご依頼内容にあわせて加工方法をご提案し、場合によっては工作機械を使い分けながら最適な方法で加工を行います。
複雑な形状でも、これまでの金属加工の経験を活かし、加工を可能にしてきました。もし加工会社をお探しでしたら、昭和製作所へお気軽にご相談ください。
汎用旋盤にて加工開始前、3次元CADソフト(CATIA)で図面を作成いたしました。
S45C材を購入し、加工を行いました。
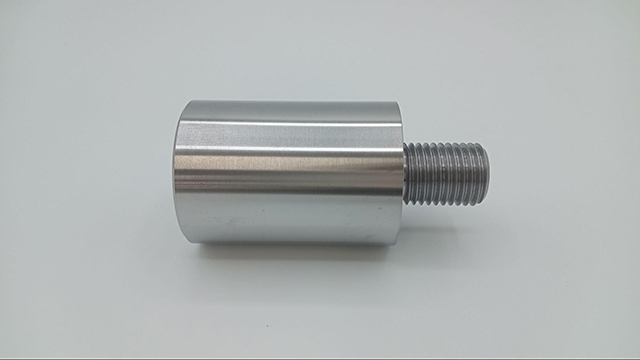
図:加工終了後、外観写真
完成までの手順について、解説をおこないます。
外径加工
はじめに素材端面にセンター穴をあけておくことで、素材の回転が安定し精度が高い加工が可能となります。
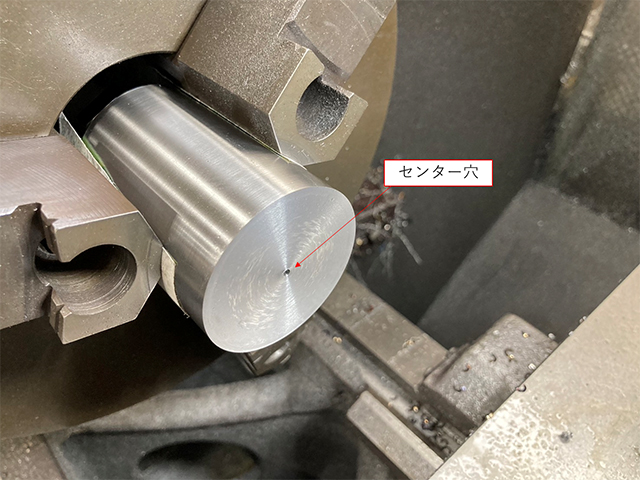
図:センター穴加工
外径加工は、その名の通り外径を削る加工方法です。外径を削るために、固定したバイト(旋盤で使用する工具)を外径に当て、ワークを回転させて段付き形状に削ります。旋盤を用いた加工方法として最も基本的な方法であり、様々な部品の製造に用いられます。
【具体的な例】
- 軸受を固定するためのシャフトの段
- 内側と外側のレースを固定するための軸受の段
- 燃焼室とクランクケースを区切るためのピストンの段
段付き加工は基本的に以下のような流れで行います。
- 旋盤に固定したバイトを、回転させたワークに当てます。
- バイトを一定の深さに送り込みながら、ワークを削ります。
- 段付きの形状にあわせて、バイトの角度や送り速度を調整します。
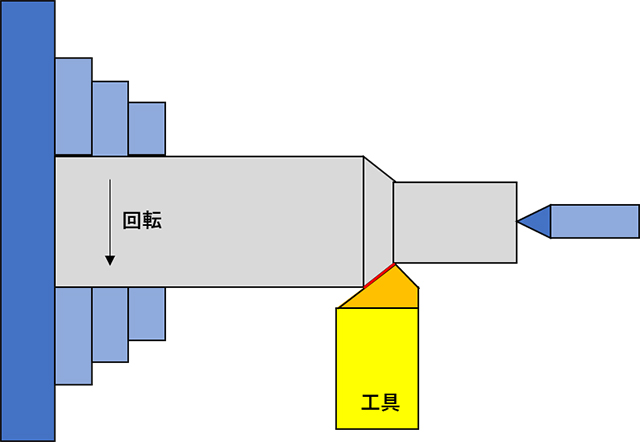
図:旋盤外径加工概略図
旋盤だけで段付き形状に仕上げることもありますが、先述したように、形状によっては旋盤以外の工作機械を用いることもあります。そのような場合は、当然ながら工数が増えてしまいます。また、旋盤による切削でも高い精度を出すことはできますが、そこからさらに精度を上げるために、切削後は仕上げを行っていきます。
今回は簡単に流れをご説明しましたが、加工が複雑になったり、工数が増えるとその分コストが上がります。コストをなるべく抑えたい場合は、工法を工夫したり、別の工作機械を使用するなどの検討も必要となるでしょう。
今回の図面では赤枠箇所を加工いたしました。
素材径Φ55からΦ50に仕上げる場合、粗加工・仕上げ加工の2段階にわけることにより、寸法や面粗度を安定させることができます。
外径のネジ下を作製する場合、呼び径に対し-0.1mmで加工をおこないます。
(例:M22の場合、Φ21.9で製作。)
呼び径=ネジ下で製作をする場合、ネジ切り後、山が尖がる為、ネジ欠けやケガをするリスクが発生します。相手製品又は部品の根元までネジがしっかり入る様、逃げ加工を実施いたします。
逃げ幅を決める際、ピッチ×1.5倍が目安となります。しかし、逃げ幅を大きくすると、ネジ山の数が少なくなる為、加減が必要となります。
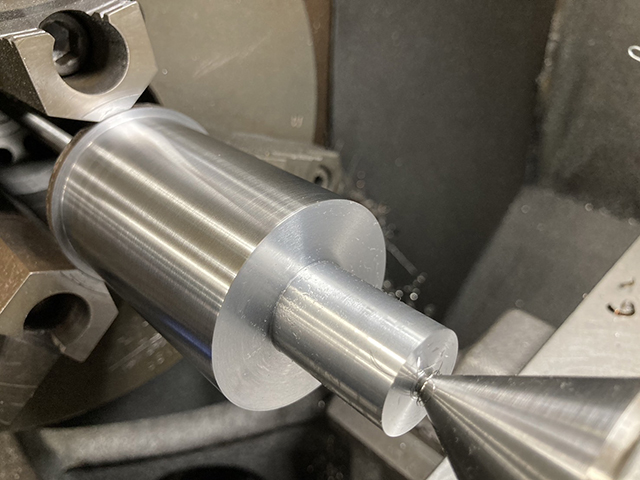
図:外径段付き加工終了
ねじ切り加工
旋盤でワークからねじを切り出す方法です。ねじ切りバイトを用いることで、螺旋状に段を付けることができます。ねじには雄ねじ、雌ねじがありますが、両方とも旋盤で加工が可能です。雄ねじはおねじ切りバイトをワークの外径に、雌ねじはめねじ切りバイトをワークの内径に当てて削ります。
主に汎用性があるタップを用いてねじ切りを行うことが多いかと思います。ねじ切りバイトを使用することで、下記利点を得ることが出来ます。
- タップ・ダイスと比べ面粗度が向上。
- 雄ねじの場合、相手部品(雌ねじ)に合わせ加工が可能。
- 雌ねじの場合、下穴に対し垂直に加工ができる。
【具体的な例】
- ボルトやナットのねじ部
- シャフトへのナット固定用ねじ
- 動力伝達用ボールねじ
今回の図面では赤枠箇所を加工いたしました。
汎用旋盤でネジ加工を行う際、送りを止めきれず切り上げミスが起こります。切り上げミスが起こると、刃物が端面にぶつかり製品が傷ついてしまいます。端面ギリギリまでねじ切りを行う際に、逃げを作ることが出来ない場合、NC旋盤、複合旋盤を使用し加工を行うことで対応可能となります。
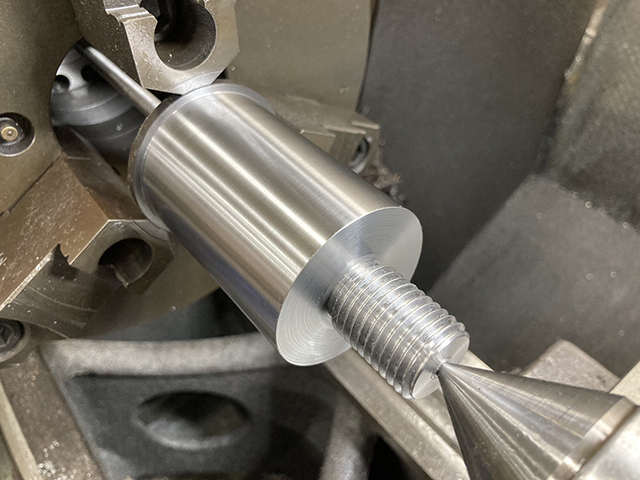
図:ねじ加工終了
端面加工
端面加工は、旋盤でワークの端面を削り取る方法です。そのため、旋盤に固定したバイトをワークの端面に当てて削り、整えていきます。この加工は、主に端面を平面に整えるときに用いられる方法で、端面に対して平行に削り取ります。
【具体的な例】
- フランジの端面に他の部品との接合面
- ガスケットの密封性を確保するための面
- 軸受を固定するための面
- ナットやボルトの取り付け面や接地面
端面加工は基本的に以下のような流れで行います。
- 旋盤に固定したバイトを、回転させたワークに当てます。
- バイトを一定の深さに送り込みながら、ワークを削ります。
- 仕上げは、面粗度に合わせて送りと切り込み量で調整します。
今回の図面では赤枠箇所を加工いたしました。
外径加工とは違い、加工途中で切削速度が変化するので、刃先が欠ける要因となります。刃物の高さを調整することにより、刃先欠け防止に繋がり、かつ中心に削り残し(ヘソ)が発生するのを防ぐことができます。
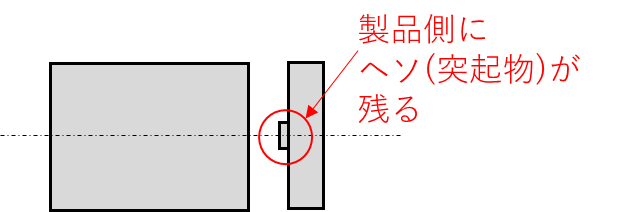
図:片持ちの状態で突っ切りを行った場合
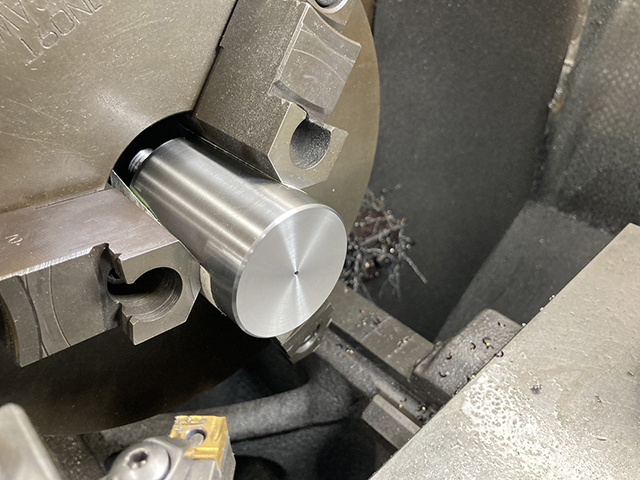
図:端面、C面取り加工終了
内径加工
内径加工も、名前の通り内径を削り取っていく加工です。ワークの内側を削って穴をあけたり空間を作ったりするため、固定したバイトも内径に設置して、ワークを回転させて削ります。内側に溝を作って段を付けることも可能です。
外径加工よりも内径加工の方が面粗度の管理が難しくなります。また、穴径が細くなるかつ穴深さが深くなるほど加工の難易度があがります。
【具体的な例】
- シリンダーにピストンを収容するための空間を作る
- 軸受にボールやローラを収容するための空間を作る
- 歯車に軸を挿入するための穴を作る
今回の図面では赤枠箇所を加工いたしました。
切削時の切りくず(切粉)が遠心力により排出されない為、注意しなければなりません。チップブレーカー(チップの先端形状)の選定や送りを早くすることで排出が可能となります。
昭和製作所ならコストダウン可能な加工方法のご提案も可能です!
段付き加工などの金属加工は昭和製作所にお任せください!
昭和製作所では、旋盤のほか、マシニングセンタや放電加工機などを保有しております。そのため旋盤に限らず、切削形状、寸法、精度、ご予算などを伺った上で、最適な加工方法を検討し、ご提案いたします。ご希望がございましたら、コストダウンのご相談も承ります。
もし「段付き形状の部品を製作したい」とお考えの方は、まずは一度お問い合わせください。弊社スタッフが、ご依頼内容にあわせてご案内させていただきます。
【お問い合わせはこちら】
連絡先:03-3764-1621
お問い合わせフォーム